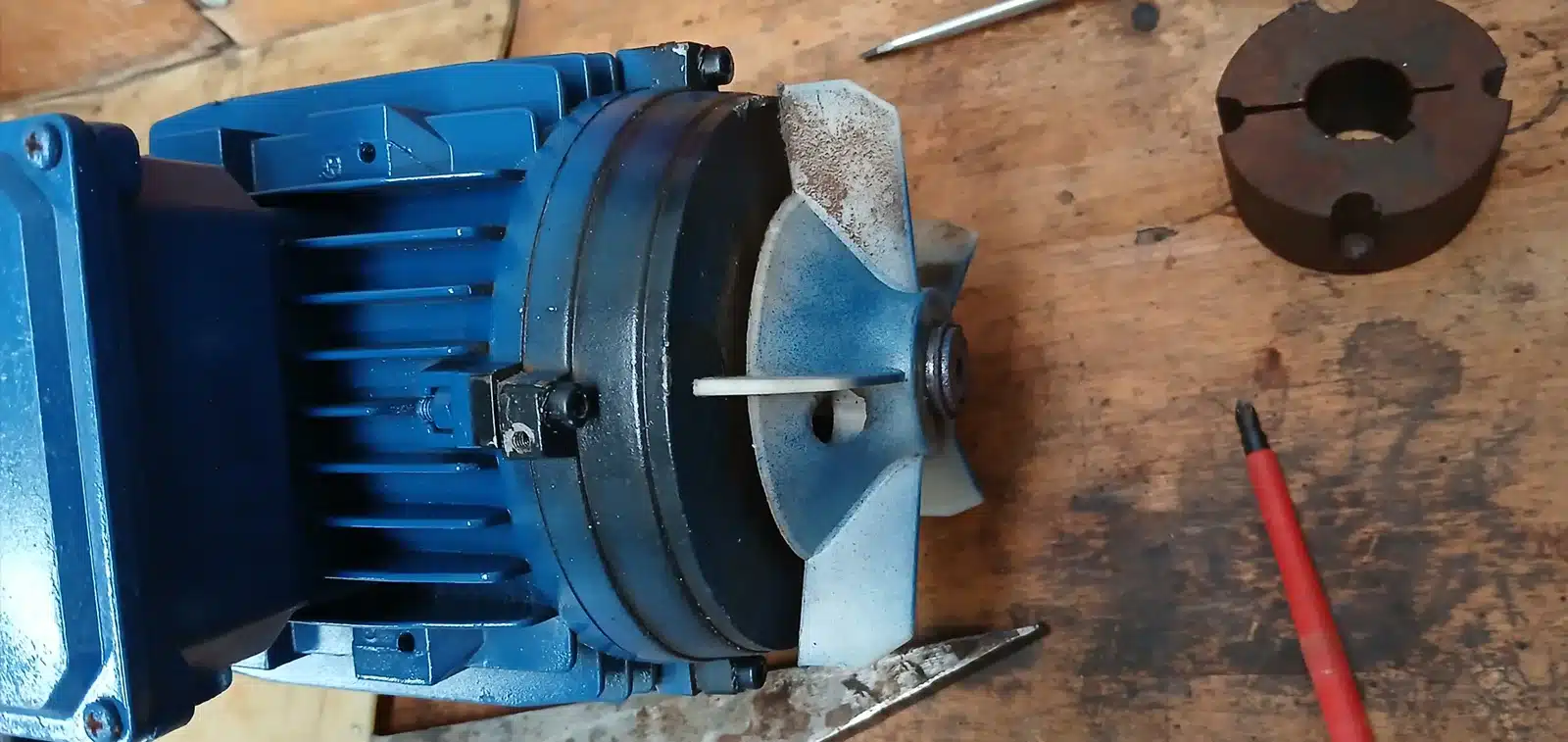
Mechanical Fitting
Mechanical/Plant Fitting is a field of mechanical engineering that deals with the maintenance of machines. The key aspect is to understand the interchangeability of mechanical parts. All machine parts are manufactured in such a manner that they are within an acceptable limit of tolerance.
Hydraulics and Pneumatics Systems
Conveyors
Pumps
Reciprocating Movement (Positive Displacement Pumps):
Rotary Movement (Rotary Pumps):
Centrifugal Movement (Centrifugal Pumps):
Oscillating Movement (Peristaltic Pumps):
Bearings
Mechanical Power Transmissions (belt, chain and fluid drives)
Belt Drives
Chain Drives
Fluid Drives (Hydraulic and Pneumatic Systems)
Summary of Applications:

The Wet Sparky LTD: Your trusted partner for innovative mechanical engineering and electrical solutions.
More than just your local Auckland electrician, we deliver increased profitability through design and innovation. Our technicians provide expert service to enhance your property and keep your operations running smoothly.
