Commercial Pumps
Transferring liquid from one place to another is an everyday occurrence in any industrial environment.
We Maintain, Repair, Install and Supply
Process Liquid Circulation
Process liquid circulation refers to the controlled movement of liquids through a system or equipment to perform tasks such as heating, cooling, filtering, or chemical processing. This circulation is essential in many industrial processes, HVAC systems, and fluid-based machinery.
Key components and principles of process liquid circulation:
1. Pumps
- Centrifugal Pumps: These are commonly used to move liquid through a system, using rotational energy to create flow and pressure. They are ideal for handling large volumes of fluid.
- Positive Displacement Pumps: These are used when more precise control of the liquid volume is needed, such as in chemical processing or dosing applications.
2. Piping and Valves
- Pipes: Used to transport liquids from one part of the system to another, ensuring proper flow paths.
- Valves: Regulate flow, pressure, and direction of the liquid. Common types include gate valves, ball valves, and check valves, which prevent backflow.
3. Heat Exchangers
- Used to transfer heat from the process liquid to another fluid (or vice versa), either to cool or heat the liquid. Common examples include shell-and-tube and plate heat exchangers.
4. Filters
- Purpose: Remove solid particles, impurities, or contaminants from the liquid to maintain process efficiency and product quality.
- Types: Bag filters, cartridge filters, or mesh strainers are used based on the type and size of contaminants.
5. Tanks and Reservoirs
- Storage for process liquids or temporary holding points between different stages in the system. These also help maintain a steady supply of liquid and manage flow rates.
6. Sensors and Controllers
- Flow Sensors: Monitor the flow rate of liquid through the system.
- Pressure Sensors: Ensure that the liquid is moving at the correct pressure.
- Temperature Sensors: Monitor the temperature of the process liquid, especially when heating or cooling is involved.
- These sensors often feed into automated control systems like PLCs, ensuring optimal operation of the entire circulation system.
Common Applications of Liquid Circulation:
- Cooling Systems: In HVAC, refrigeration, or industrial cooling, liquids like water or coolant circulate to remove heat from processes or equipment.
- Heating Systems: Used in boilers, heat exchangers, and process heaters to distribute hot water or other liquids to maintain specific temperatures.
- Chemical Processing: Liquids are circulated through reactors, mixers, or separators to facilitate reactions, blending, or filtration.
- Water Treatment: Circulation of water through filters, membranes, and disinfection units to clean and purify water in municipal and industrial applications.
Benefits of Proper Liquid Circulation:
- Efficient Heat Transfer: Ensures that heating or cooling processes are optimized.
- Consistent Fluid Quality: Helps maintain fluid properties by preventing stagnation and ensuring contaminants are filtered out.
- Stable Process Control: Provides better control over temperature, pressure, and flow, leading to more consistent process outcomes.
- Equipment Longevity: Reduces wear and tear on pumps, piping, and other components by maintaining a steady flow and reducing the risk of blockages.
Process liquid circulation is a critical function in industries like chemical manufacturing, power plants, HVAC, food processing, and pharmaceuticals, ensuring efficient and reliable operation of fluid-dependent processes.
- Lift well pumps.
- Sewage transfer.
- Sump pumps.
- Pump Control and protection.
- Retention tank transfer.
Dosing Pump Systems
Dosing pump systems are specialized systems designed to accurately inject a specific volume of liquid (usually chemicals) into a process stream or tank. They are essential in various industries for applications like water treatment, chemical processing, pharmaceuticals, and food production. Here’s an overview of their components, operation, types, and design considerations:
Key Components of Dosing Pump Systems
- Dosing Pump: The core component that delivers the precise volume of liquid. They can be either:
-
- Positive Displacement Pumps: Commonly used for dosing because they provide accurate flow rates regardless of pressure variations.
- Diaphragm Pumps: Often used for corrosive or viscous fluids, ensuring no contact between the fluid and the pump mechanism.
- Control System: Regulates the operation of the pump based on input from flow meters, pressure sensors, or timers. Can be manual or automated (e.g., PLC-controlled).
- Piping and Valves: Connect the pump to the process. Valves may include check valves (to prevent backflow) and flow control valves (to adjust the flow rate).
- Injection Point: The location where the chemical is introduced into the process stream, which may require special fittings or nozzles to ensure proper mixing.
- Storage Tank: Holds the chemical to be dosed. It should be compatible with the chemical properties and designed for easy filling and maintenance.
- Safety Equipment: Includes leak detectors, pressure relief valves, and emergency shut-off systems to ensure safe operation.
Types of Dosing Pumps
- Diaphragm Pumps: Offer excellent chemical compatibility and leak prevention. Suitable for low to medium flow rates and high pressures.
- Gear Pumps: Provide a continuous flow and are suitable for high-viscosity fluids.
- Peristaltic Pumps: Ideal for sterile or abrasive fluids. The fluid only contacts the tubing, reducing contamination risk.
- Solenoid-Driven Pumps: Commonly used for smaller dosing applications due to their compact size and affordability.
- Electromagnetic Pumps: Suitable for high precision and low flow applications, often used in laboratory settings.
Design Considerations
- Flow Rate and Pressure: Determine the required dosing rate and the pressure the pump must overcome. This informs pump selection and sizing.
- Chemical Compatibility: Ensure all materials in contact with the fluid are compatible with the chemical being dosed to prevent degradation or leaks.
- Accuracy and Repeatability: Consider the dosing accuracy required for the application, often expressed as a percentage of the flow rate.
- Control Method: Decide on the control system—manual, timer-based, or automated. Automated systems can improve precision and reduce operator error.
- Installation and Maintenance: Plan for easy access to the pump and components for maintenance, calibration, and troubleshooting.
- Safety Measures: Implement safety features to handle chemical spills, leaks, or over-dosing. Include alarms and emergency shutdown options.
Applications
- Water Treatment: Dosing of chlorine, coagulants, or pH adjusters in municipal water treatment plants.
- Chemical Processing: Precise injection of catalysts, solvents, or reactants in chemical manufacturing.
- Food and Beverage: Dosing of flavors, preservatives, or cleaning agents in food processing.
- Pharmaceuticals: Accurate dosing of active ingredients in drug formulation.
Dosing pump systems are crucial for maintaining process efficiency, product quality, and safety across various industries, providing precise control over chemical injection processes.

The Wet Sparky LTD: Your trusted partner for innovative mechanical engineering and electrical solutions.
More than just your local Auckland electrician, we deliver increased profitability through design and innovation. Our technicians provide expert service to enhance your property and keep your operations running smoothly.
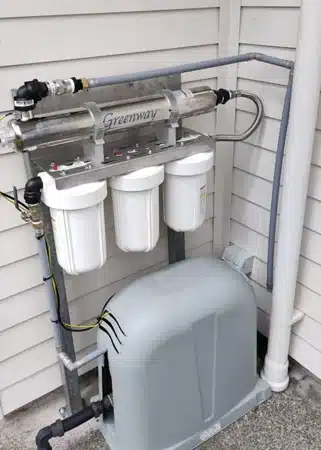